Overview: Conversations on the IoT Tech Expo 2018 conference floor
by Brad Canham
Sometimes conferences provide developers with the technical meat they’re looking for. At other times conferences provide the core movements in a marketplace the strategists – VCs, product managers, marketing people – are looking for. At the Nov. 28-29, 2018 IoT Tech Expo event in Santa Clara, the show floor dialed the marketplace focus tighter than ever on predictive maintenance use cases.
The focus especially involved industrial IoT PdM use cases, like the one Cassia Networks has with ABB Ability Smart Sensor solution. As a whole, the IoT Tech Expo 2018 conference floor conversations were a marked contrast from the event’s 2017 rush of cryptocurrency entrepreneurs on their way to bank Bitcoin billions. So, what are the early factors influencing PdM IoT?
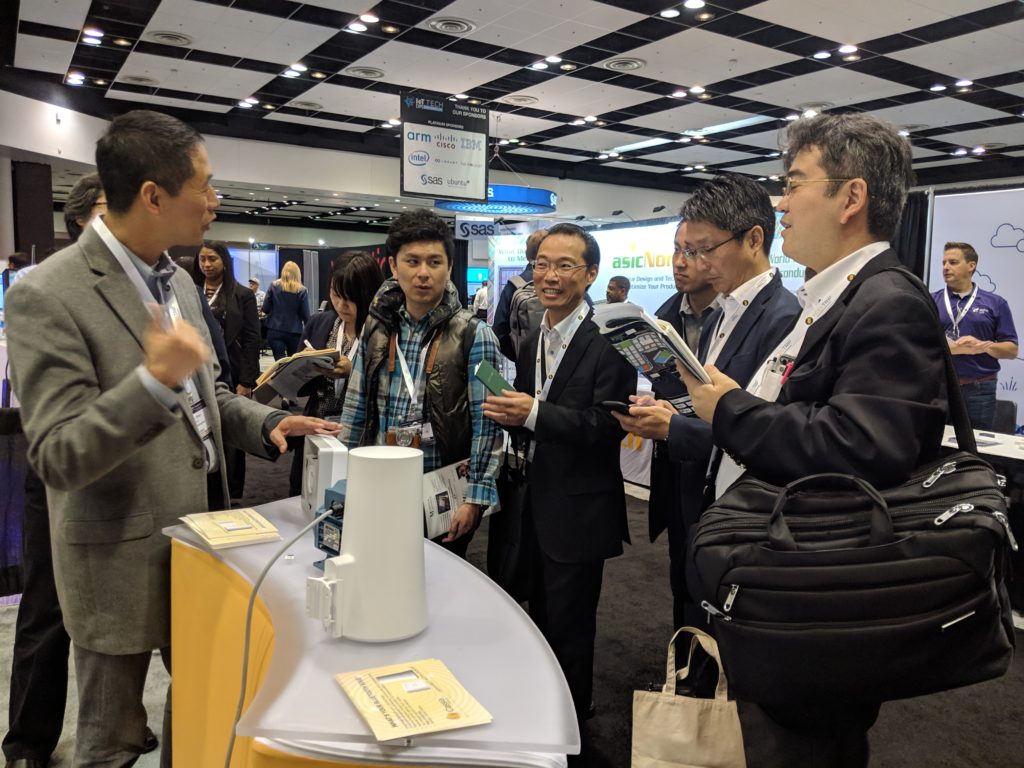
“What is the condition of a thing?” is the essence of PdM IoT. Lets get right to market factors to consider regarding PdM IoT.
PdM IoT takeaways
There are two fundamental types of PdM IoT – 1.) condition monitoring for efficiency, and 2.) two, regulatory and compliance PdM IoT for meeting regulatory requirements and providing proof of compliance.
Among other factors, remember regulatory and compliance PdM IoT is different than standard “uptime” or maintenance monitoring. Broadly speaking, regulatory requirements continue to increase, however, compliance and compliance enforcement varies significantly by country, state, county and city complicating back end data management.
As for predictive maintenance associated with machine health PdM IoT, in addition to uptime and health of individual machines, the energy savings associated with the overall factory efficiency involving uptime and machine health is significant.
Rise of the “Secondary” machines: PdM IoT for the ignored
“Secondary”machine vendors are seeking insights into their end customers’ factory floors.
Vendors of “secondary” machines – often involved in supply chain delivery, or infrastructure, but not production – were previously ignored by condition monitoring solutions. Initial condition monitoring bypassed secondary machines due to cost or complexity, but are now seeking insights into how to create “stickiness” and added-value for their machines. These secondary machine vendors include those who supply consumables and lower energy engines, and include filters, liquids, low-voltage engines, pallets, batteries, or low horse power motors, pumps, actuators etc…
As these machines are often sold to factory by dealer channels, the vendors lack direct customer insights to how their machines are used and performing (or not performing) on the factory floor. Often these machines are ignored by dealers (as well as maintenance personnel and plant engineers) as they are not the core revenue generating machines for dealer channels. Vendors of these kinds of machines are increasingly seeking low cost PdM IoT (often using BLE) to find a “way in” to their factory customers.
When the “Secondary” machines break down, we break down.
Secondary machines, like consumable elements and filters, can cause problems with “primary” production machines and create a cascade of “scheduling” issues. At present, these secondary machines, (not already attached to SCADA system or an industrial production environment) are a major opportunity for both for uptime as well as for regulatory and compliance-related PdM IoT.
Market maturity gap in secondary machine PdM IoT adoption.
Problems due to unscheduled maintenance and down time are well known. Recently a manufacturer of a “secondary” machine – who asked for anonymity – performed a rough survey of its customers. Their results noted 88% of the owners of its secondary machines were interested in performance monitoring; 87% were “interested” in alerts to change out secondary machine components based on condition.
In general, machines which process factory consumables are typically not viewed as revenue generating machines. In fact, these machines are often ignored, and yet they can often operate more efficiently, thereby reducing power costs. Increasingly they are tasked to provide unique environmental and operating data. Why? First, pulling data from such a machine using a PdM IoT solution can help the secondary machine manufacturer create further “stickiness” in the factory environment as the base offering. For example, with data gathered as part of a PdM IoT solution, additional return on investment (ROI) may be quantified in new ways for a secondary machine. Then, manufacturers of secondary machines can find out more about what the factory plant engineer wants to accomplish (higher efficiency, lower cost) and determine what unique, added-value data (environmental or operating condition info) the secondary machine can provide to meet that need and which the plant manager may be willing to pay for.
The above insights were gathered from the IoT Tech Expo 2018 event conference trade show. Firstly, the number of participants interested in PdM industrial IoT was a marked change from the event in 2017. Also, the “vibe” was much more use case specific with Bluetooth networking PdM IoT for this broad category of “secondary” machines on the rise.
In conclusion, the simple takeaway from the IoT Tech Expo 2018, is in 2018 companies are looking for a way to track the condition of existing things. Yes, there is also interest in building “new” things and tracking “where things are.” These are a part of the Bluetooth networking IoT use cases currently underway. But, PdM IoT, the ability to know the condition of a thing, and to use that data to build models from which “predictions” can be made was a topic of keen interest at IoT Tech Expo 2018.