Today’s Industrial IoT enterprises operating in hazardous environments not only need to safeguard their equipment, but they also need to protect their workers. A slight spark in an oil & gas field or chemical plant could trigger a fire or explosion resulting in damaged equipment and the environment or even worse, loss of life. As a result, today’s smart manufacturers are taking the necessary precautions in deploying specialized equipment for hazardous environments but also making sure they are fully certified with the appropriate ratings. Let’s give a quick overview of the different hazardous area classifications, the different zones and classes and why they’re important.
Hazardous Area Classifications and Regulating Agencies
For starters, an industrial area is considered a hazardous area when it contains three components: A flammable substance (this can be a gas, liquid, or solid), an oxidizer, and a source of ignition (i.e., a spark or open flame). Essentially, hazardous area standards require the use of specialized equipment certified for use in these areas that have the above three components that may cause an explosion. The goal of hazardous area equipment is to prevent an explosion, but it’s important to note that different types of equipment have different uses and applications. There are several methods today’s manufacturers are using to prevent a device or equipment from causing an explosion. First, is to contain the explosion with an explosion proof device or enclosure. The purpose of the enclosure is to protect it from extreme heat so that in the event of an explosion, the enclosure would encapsulate the device and contain it to avoid further spread. The second approach would involve removing the possibility of a spark or other source of ignition. This is usually accomplished by keeping the temperature low and keeping all electronics secure so it does not generate enough heat or electrical current to create a combustion. The third approach is to isolate the explosive substance from anything that could possibly ignite that material.
There are different organizations and agencies dedicated to guiding various industries towards implementing best practices. These organizations will require, among other things, the use of hazardous area equipment in areas which possess the three components necessary for an explosion. In North America, traditionally, FM (Factory Mutual) and UL (Underwriters Laboratories) provide standards, testing and certification in the United States while CSA (the Canadian Standard Association) does the same for Canada. More recently, UL, FM, and CSA have all implemented programs allowing certifications to be valid in both countries.
Outside of US and Canada, organizations such as ATEX (Appareils destinés à être utilisés en ATmosphères Explosives) or in English (Devices intended for use in explosive atmospheres) as well as the IEC (International Electrotechnical Commission), provide standards that are recognized internationally. Many North American companies will certify their products to ATEX and/or IEC standards in order to make them valid for their global business operations. It’s important to note that ATEX and IEC classify equipment for use in hazardous areas a little differently than UL, FM and the CSA. Through testing, a piece of equipment is assigned to an area classification, zone or division, equipment group and temperature class.
What are the different classes and zones?
Class I could be an oil refinery or offshore oil rig. Class II might be a grain silo or coal mine and Class III could be a woodworking facility or paper mill. Next, a division or zone is assigned to the product. Zones usually include the area classification with the zone description. Zone 0 for example, describes an area in which a combustible gas will be present continuously. Zone 1 is an area in which an explosive gas atmosphere is likely to occur in normal operation and Zone 2 describes an area in which an explosive gas atmosphere is not likely to occur in normal operation and, if it does, will only exist for a short time.
Why is it important to certify a product?
As mentioned above, a device or product that has been tested rigorously and certified is fundamental to ensuring safe operations and protecting workers. Once the device/product bears the agency’s mark, equipment manufacturers and installers can rest assured that the product is approved for use in hazardous areas. What may seem like a hodgepodge of letters and numbers on a label as seen in the image below, this information is critical to ensure the device is approved and safe for any hazardous area application. Being able to understand the specifications and classifications of hazardous area products is important for any industrial IoT manufacturer operating in these environments.
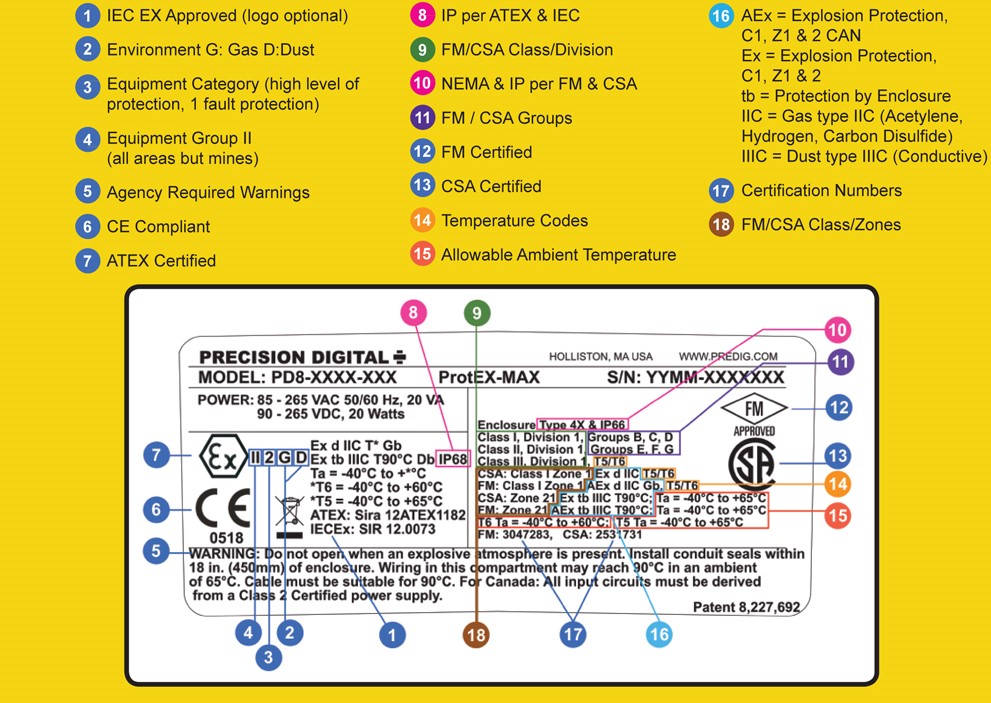
Did you know that Cassia’s latest ATX2000 Bluetooth gateway is uniquely designed for hazardous areas? The ATX2000 Bluetooth gateway is fully certified for Zone 2, 22 and Division 2 areas. The IP66 and NEMA 4 rated gateway allows today’s industrial manufacturers to achieve the long range connectivity and scalability needed to successfully deploy their industrial IoT applications.